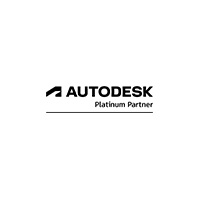
Carolin Werthmann
Gegen den Strom – 3D-gedrucktes Boot revolutioniert den Bootsbau
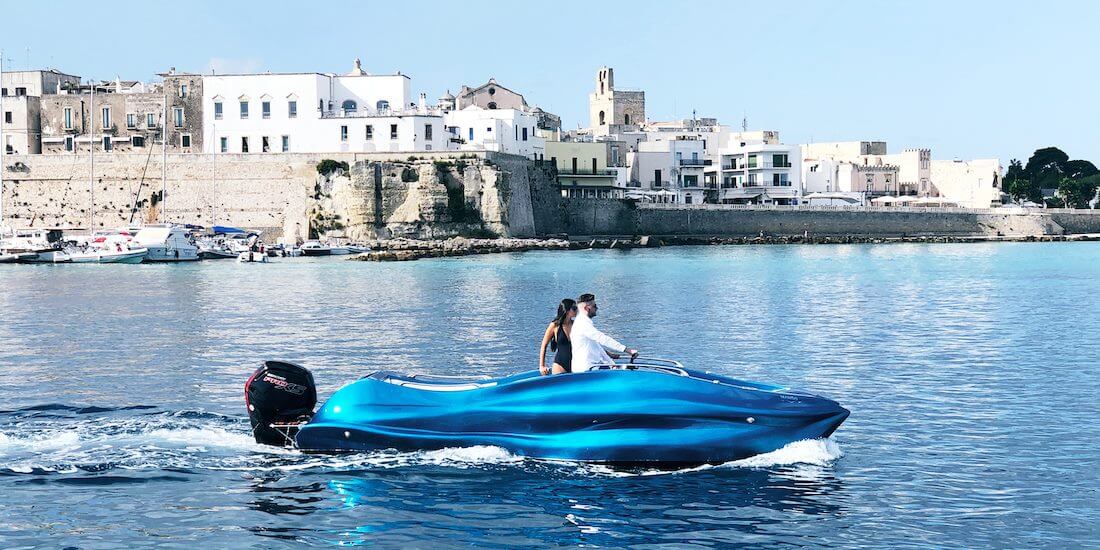
Es heißt, Gabriele Natale wollte schon immer ein Boot produzieren wie das, das er nun mit seinem Team realisiert hat. Es trägt den Namen „MAMBO“, eigentlich Motor Additive Manufacturing Boat, aber eine passendere Abkürzung könnte es kaum geben für etwas, das aussieht, als habe es sich den Hüftschwung kubanischer Musik einverleibt. Markant sind seine wellenförmigen Außenseiten, die Einkerbung, die es zum Heck hin schmaler werden lässt, sich wie zu einer Flosse verengt. Mambo ist der Hai unter seinesgleichen, der Raubfisch, der anderen Booten die Show stiehlt, weil er nicht nur eigenartig aussieht, sondern auch eigenartig hergestellt wurde.
Während dieser Text entstand, schlummerte Mambo noch in der Werft von Catmarine, einem Bootsbauer in einer der südlichsten Ecken Italiens vor dem Ionischen Meer. Dort sollte das Boot, vor seiner Präsentation auf der internationalen Bootshow in Genua, im Wasser getestet werden. Auf der Messe wird es als Beispiel dafür stehen, wie stark das Design von seinem Fertigungsverfahren abhängt und was möglich ist, wenn die Hersteller sich emanzipieren von traditionellen, wenn auch über Jahrzehnte erprobte Methoden. Mambo ist ein 3D-gedrucktes Boot aus glasfaserverstärktem Kunststoff. 6,5 Meter lang und 2,5 Meter hoch, 800 Kilogramm schwer. Es ist nicht das erste seiner Art, aber eines, das die Ästhetik auf ein neues Level hebt.
3D-Druck statt Handauflegeverfahren
Gabriele Natale ist Mitgründer des italienischen Start-Ups Moi Composites. In seiner Forschungsarbeit am Polytechnikum in Mailand, einer staatlichen ingenieurwissenschaftlichen Technischen Universität, beschäftigte er sich mit durchgängig gedrucktem Glasfaserverbund (Continuous Fiber Manufacturing), einem 3D-Druckverfahren, von dem er sich eine größere Vielfalt an Designmöglichkeiten versprach. „Es fehlt Bootdesignern nicht an Ideen und Kreativität, sondern an den Methoden, sie umzusetzen“, sagen er und sein Kollege Michele Tonizzo, mit dem er Moi Composites gründete.
Gut sichtbar: Der hintere Teil des Bootes erinnert an die Form des Katamarans, der aus zwei Rümpfen besteht.
Vor allem in der klassischen Bootsmanufaktur ist man eingeschränkter, arbeitet oft noch im Handauflegeverfahren mit Formen, in die Endlosfasermatten Schicht für Schicht eingelegt, gebacken und ausgehärtet werden. „Unsere Vision ist, Fertigung mit Kompositen neu zu definieren und die Möglichkeiten zu revolutionieren, wie Produkte entstehen und gestaltet werden“, sagen sie. Durch das additive Fertigungsverfahren sparen sie Material, mit den vorangehenden digitalen Entwürfen suchen sie nach ungewöhnlicher Ästhetik, nach einer, wie sie es nennen, „bislang unmöglichen Form“ und danach, gestalterische Limits zu sprengen.
Das Design entstand in Fusion 360, die Prozessverarbeitung und Maschinenparameter wickelte Netfabb ab und Powermill kam für die Robotiksteuerung zum Einsatz.
Zu Beginn schloss sich Moi Composites mit mehreren Partnern zusammen, darunter Autodesk, das die Software Fusion 360, Netfabb und Powermill sowie diverse Simulationsprogramme beisteuerte. Der eigentliche Druckprozess startete ein halbes Jahr später, und wenn es nur darum ginge, etwas zu drucken, sei es auch noch so komplex wie die Form von Mambo, wäre das alles ziemlich schnell erledigt gewesen. So erinnert sich Dominique Müller, Materialwissenschaftlerin und Forschungsingenieurin bei Autodesk, die das Projekt von Beginn an begleitete und mit der notwendigen Software betreute. „Wenn wir nicht so viel rumgespielt hätten, wäre das komplette Boot in wahrscheinlich drei Monaten gedruckt gewesen“, sagt sie. Mit „rumspielen“ meint sie das Tüfteln am Design.
Kombination aus Katamaran und Schalenboot
Sie simulierten, wie sich das Boot im Meer verhalten und wie es entsprechend aussehen müsste, um sich den stürmischen Bedingungen angemessen fortbewegen zu können. Außerdem hatten sie sich zwei verschiedene Bauarten zum Vorbild genommen. Das klassische Schalenboot und den Katamaran. Sie wählten eine Kombination aus beidem, Michele Tonizzo nennt das Y-förmige „Arcidiavolo“ des britischen Bootdesigners Renato „Sonny“ Levi als konkrete Inspirationsquelle. Der hintere Teil von Mambo erinnert nun an die zwei Rümpfe eines Katamarans, der vordere Teil entspricht dem Bug des Schalenboots. Die geschwungene Form an der Seite, der Hüftschwung, ist weniger funktional, als eine ästhetische Entscheidung.
Aber nicht nur Design und Herstellungsverfahren sollen das Boot interessant machen. Michele Tonizzo sagt, das Projekt sei beispielhaft für dezentrale Manufaktur. Denn Mambo wurde über drei Länder hinweg entwickelt und produziert. Die Software-Expertise kam aus Deutschland, gedruckt wurde in Birmingham und Mailand – also im britischen Technologiezentrum von Autodesk und in der italienischen Werkstatt von Moi Composites.
Die Produktion und Kommunikation lief über die Cloud, sodass Moi steuern und kontrollieren konnte, was in Birmingham geschah. Das klingt erstmal nach zusätzlichem logistischem Aufwand, und tatsächlich war die Aufteilung zunächst eine notgedrungene Lösung, weil schlicht das Equipment und der Platz fehlten, das Boot allein in Mailand zu drucken. Moi besaß zu diesem Zeitpunkt zwei fest installierte, mehrachsige Robotikarme, mit denen die Teile gedruckt werden konnten. Durch die teilweise Auslagerung der Produktion nach Birmingham, wo es einen dritten Roboter gab, konnte gleichzeitig gearbeitet werden. Noch besser wäre ein Roboter auf Schienen, merkt Dominique Müller an. Dann könnte man das Boot in einem Stück drucken.
Generative Design: Der Paradigmenwechsel in der Konstruktion?
Erfahren Sie in unserem Quick Value Guide Generative Design mehr darüber, welche Vorteile die generative Fertigungsmethode schon heute bietet und wie sie die Zukunft der Konstruktion mitgestalten wird. Informativ, leserfreundlich und technisch kurzweilig.Anmerkung der Redaktion: Die im Artikel dargestellten Bilder sind ausnahmslos von Autodesk und Moi Composites.
Nehmen Sie Kontakt mit uns auf
Daniel Pasing, Customer Success
Sie möchten mehr über unsere Produkte und Lösungen erfahren? Unser Customer Success ist für Sie da.